Different from aftermarket parts development, suppliers only make qualified products according to clients' drawing, OE parts development often only has a simple prototype design and working conditions requirements, which put forward higher requirements on the ability of supplier's collaborative development.
We recently developed a fuel filter for an internationally renowned Off-Road vehicles brand, and we were responsible for the entire product development process, from drawing design, supplier selection, prototyping and production. A real story: from Zero to Hero.
Supplier Selection& Drawing Design
We identified several qualified auto parts factories and audited every aspect of each and issued the dolphin reports.
The report contains the following:
* Supplier evaluation form
* Facility tour
* Shotting list
* QCLDM scoring sheet
...
This report let client know the most real conditions of the factories.
As there are no factories on the market that produce small size fuel filters, we selected a factory which is specialized in production fuel filters for our client. Although this factory has never produced such a small fuel filter, with our help they designed the drawings with their rich manufacturing experience.
Performance Testing
After producing the sample according to the design drawing, we tested the performance of the sample according to the requirements from the client.
Because the testing equipments in the factory are insufficient, we completed all the performance test by contacting the third party test organization, and finally issued the professional test report for the client. This step is to ensure that the product meets the performance parameters and working conditions required by the client.
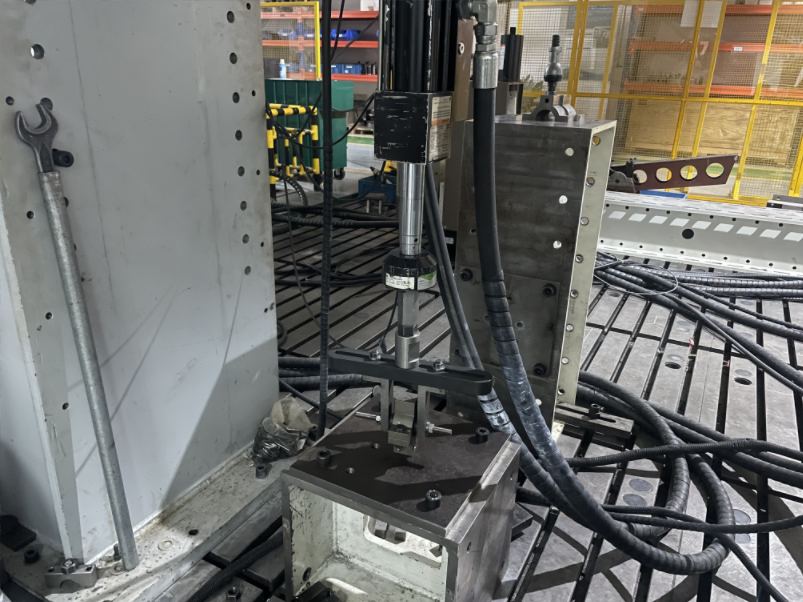
After the report came out, we found that the bursting strength of the product was not up to the standard. Our engineers found that the problem was due to the formula and dosage of the glue. And we did a lot of experiment, we finally solved this technical difficulty after 6 weeks hard work.
Process Control
During the trial production stage, our QA engineer and service assistant followed up the production in the factory for one month, and feedback to the client on-site problems at any time, so that the client can always know the true information. Through continuous improvement and problem solving, we finally completed the trial order on time.
During the bulk production stage, our team will have video meetings with the factory together when the client have questions, and went to the workshop to verify the improvement measures on site.
The DEWIN team is the eyes of the client in the factory, we providing the most accurate information and assisting the factory to solve problems, improve processes and meet client´s requirements.